Supply chains, safety protocols hobble US factories
Some US factories are looking for alternative suppliers
Manufacturers emerging from weeks in hibernation during the coronavirus pandemic are accelerating production with jumbled supply chains and less efficient plants, making it harder to rebuild the weakened U.S. industrial sector.
Some U.S. factories are looking for alternative suppliers to compensate for plants that remain closed or are overwhelmed by orders for items in high demand. Other companies say new protective equipment and procedures to add space between workers will weigh on their profits and productivity.
CHINA DELAYED RELEASING KEY CORONAVIRUS INFORMATION, FRUSTRATING WHO
Meanwhile, many manufacturers are encountering bleak conditions in industrial markets that have shrunken with the contracting U.S. economy. Durable-goods orders in the U.S. are at the lowest level in a decade, and surveys of purchasing managers at manufacturers in the U.S., Europe and Asia suggest any recovery in the months ahead could be tentative.
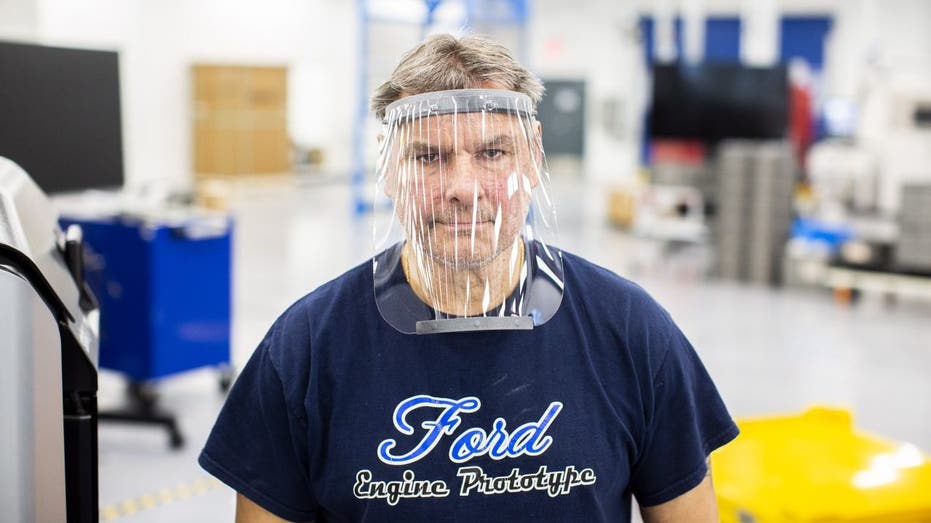
REDFORD, MI. Mar. 24, 2020 – Dave Jacek, 3D printing technical, wears a prototype of a 3D-printed medical face shield printed at Ford’s Advanced Manufacturing Center. Photo courtesy: Ford
Other companies say they haven't been able take advantage of markets where demand has been more resilient. Ardisam Inc., which makes fishing and gardening equipment that is in high demand from people spending more time outdoors, hasn't been able to get enough parts for fence-post diggers and chicken pluckers from factories in China.
Chief Executive Michael Furseth said Ardisam's sales would have been 25% higher this spring if the Wisconsin-based company had stock on hand to fill all the orders it received. "You are just behind, and you can't catch up," he said.
Wanxiang America Corp., an Illinois-based unit of one of China's largest auto-parts makers, restarted more than 20 plants in the U.S. last month after undergoing some modifications to reduce contact between employees.
CORONAVIRUS HAS CITI CONSIDERING SUBURBAN OFFICES: REPORT
Pin Ni, president of Wanxiang America, said the idling of auto production in the U.S. bought time for Wanxiang's own supply chain in China to recover from lockdowns imposed on factories there earlier this year. But he said he expects some suppliers to go out of business this year because they won't be viable at lower production rates anticipated across the auto industry.
"Any one failure is going to impact everybody," Mr. Pin said. "We're all co-dependent on each other."
General Motors Co. last month delayed plans to increase production of pickup trucks because of a shortage of parts from Mexico. Many manufacturing plants in Mexico, which surpassed China as the top trading partner to the U.S. last year, were ordered closed early during the pandemic. A gradual reopening of plants started Monday based on the level of contagion recorded in each of the country's 32 states.
Ticker | Security | Last | Change | Change % |
---|---|---|---|---|
GM | GENERAL MOTORS CO. | 55.59 | +0.09 | +0.16% |
China has largely reopened its industrial economy, but many U.S. buyers are only now using items that would have been made and shipped from there earlier this year, when the economy was locked down and cargo traffic had collapsed.
For other U.S. companies, strained overseas supply chains have created opportunities to fill orders domestically. Littlestown Foundry Inc., a Pennsylvania-based producer of aluminum-cast components for electrical equipment, said it obtained about $350,000 worth of orders in the past year from a customer that wanted to shift about $3.5 million worth of work annually to the U.S. from China.
"The good work we gobbled up right away," said Glen Morrell, Littlestown's vice president.
Litttlestown last week resumed shipments of aluminum parts to Mexico, where a plant in Juarez that finished the parts had been idled by government coronavirus restrictions. As production accelerates, Littlestown is stockpiling more aluminum ingots than usual because deliveries have been less reliable.
"I used to play inventories a lot closer than I am right now," he said.
Other companies have become more cost-conscious as disrupted supply chains and new spending on safety protocols erode profits. O-I Glass Inc., the biggest domestic producer of glass bottles, said it is using more expensive raw materials to make glass because of a shortage of recycled glass. The volume of recycled glass from states with deposits on beverage bottles plunged by two-thirds in April after redemptions on empties were suspended as a safety precaution for retail workers.
GET FOX BUSINESS ON THE GO BY CLICKING HERE
"We've built our supply chains based on recycling," said Randy Burns, O-I's chief sustainability officer.
The virus has driven up costs and shaved profits for companies that haven't experienced supplier delays or falling sales. Housewares company Honey Can-Do International Inc. said its overhead costs have climbed, despite minimal disruption in shipments of kitchen, bathroom and home storage products from China, Vietnam and elsewhere in Asia.
CLICK HERE TO READ MORE ON FOX BUSINESS
Chief Executive Steve Greenspon said the company's Illinois distribution center is less efficient now because operations have been reconfigured to separate employees. For instance, the company is only allowing one worker at a time to unload shipping containers, rather than the two people that usually work together inside the cramped metal boxes.
"The container takes twice as long to unload," he said.