Ports in a Storm: Looming Strike Could Cost Billions
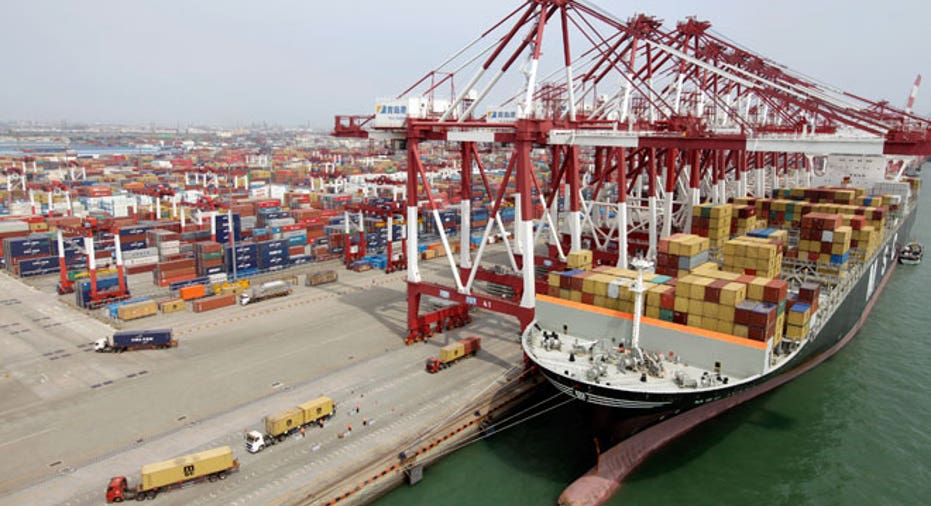
A deadlock between U.S. port workers and their employers could result in a massive strike next month that would bring activity in major ports along the East and Gulf Coasts to a near stop.
It’s a major concern, as a strike of this magnitude, which would have the potential to shut half of all U.S. ports starting Oct. 1, would have the ability to break the retail supply chain, shrink inventories and bring assembly line operations reliant on imported parts to a halt.
Striking at the heart of a still fragile economy, it would all come as the holiday season begins to ramp up, a mere 30 days before the U.S. presidential election.
“What’s at stake here is significant,” said Greg Johnsen, co-founder and chief marketing officer of GT Nexus, a cloud supply-chain platform developer. “It’s just really unfortunate timing.”
If negotiations between the International Longshoremen’s Association that represents the port workers, who are fighting for fairer wages and job security as automated operations threaten their jobs, and the Maritime Alliance, which represents port operators, fail to end in a resolution by the Sept. 30 deadline, strikes may cripple operations at busy hubs like New York, New Orleans, Boston and Houston that together manage hundreds of billions of dollars in U.S. trade each year.
It is going to devastate the U.S. economy unless some action is taken.
Port strikes of this magnitude have the potential to impact $22 billion in trade over a two-month period, including both imports and exports, according to data compiled by trade intelligence company Zepol and first reported by World Trade 100. Analyzing data from October and November 2011, nearly $18 billion in Gulf Coast and East Coast imports and about $4 billion in exports would be affected.
A shutdown -- if it happens -- would cause a major bottleneck and serious infrastructure and supply-side disruptions, Johnsen said, just as imported holiday items are scheduled to sail into port.
The implications would reverberate across suppliers, retailers and shipping companies. If it were to stretch long enough, a supply shortage could erupt just as demand ramps up, leading to a shortage of inventory -- if companies haven’t prepared -- that could ultimately translate to higher prices during the busiest season for retailers.
The Retail Industry Leaders Association (RILA) is calling for a resolution between the worker’s main union and their employers, noting that a “disruption of this magnitude would be devastating to the retail industry and would have severe consequences for the U.S. economy.”
While discussions that halted last week resumed again on Thursday, there is no guarantee a deal will be reached by the Sept. 30 deadline. Highlighting the urgency, the National Retail Federation said it is critical that negotiations continue without disruptions to the supply chain even if the talks pass through the deadline.
Nevertheless, the threat has forced retailers to kick in gear their contingency plans that include shipping items to different ports, using alternate ways of shipping such as airfreight and expediting shipments to boost buffer inventory.
The NRF, which has more than 9,100 members, said most companies that would be affected if a strike were to occur have started looking into alternative plans, particularly since a shipping cycle can take weeks.
“We believe most are prepared as they have all been paying attention to the negotiations from the outset,” NRF Vice President of Supply Chain and Customs Policy Jonathan Gold said.
While most retailers would not comment on their contingency plans or the union talks, Target (NYSE:TGT) said that it is “actively monitoring the port situation and has a well-defined contingency plan in place.”
However, in the face of a potential strike, ensuring that products will be on the shelves in time for holiday promotions to meet growing demand that typically comes in the weeks leading up to Black Friday, retailers will have to pay a price.
It will cost them money to expedite plans, use different ports on the West Coast or in Canada, keep additional inventory at distribution centers and organize additional transportation to handle the increased loads.
Retailers “planned for the year what their transportation costs were going to be,” said Mickey North Rizza, vice president of strategic services at BravoSolution and a long-time supply chain consultant. If the strikes caused them to alter their plans, any additional transportation costs above a half a billion dollars would be “significant,” she said.
Of course, a port slowdown would impact not only retailers, but without critical supplies and components being shipped from abroad, assembly line activity could slow and that could impact when U.S.-assembled products hit the shelves.
That might cause orders from manufacturers like Nike (NYSE:NKE), Apple (NASDAQ:AAPL) and Victoria’s Secret parent Limited Brands (NYSE:LTD) to be cancelled, which would impact jobs and revenues across the board, from the suppliers and cargo shippers to the largest retailers like Wal-Mart (NYSE:WMT), Target and Macy’s (NYSE:M).
“If it shuts down, nothing comes in and nothing goes out,” Gold said. “All jobs are impacted … it’s much bigger than the ports themselves.”
As the world continues to become more integrated and even more production is shipped to fast-growing emerging markets like China, the need for better communication, integration and preparation among the entire network -- from orders and mineral sourcing to development, shipment and selling -- has been underscored.
“The tsunami in Japan was the catalyst to get companies thinking more about risk,” said Gary Barraco, director of product marketing for ecVision, noting that companies slow to react to the natural disaster in Japan saw shipments of anything from phones to automobiles crippled for days, in some cases even weeks or months.
“You never used to see C-level executives focused on the supply chain, but now they are [and] supply chains have become tighter,” he said.
This has led to an increase in adoption of cloud-based communication platforms and technologies such as those made by ecVision and GT Nexus that allow people across the dozens of layers of any particular supply chain to keep tabs on the various stages of production and shipment.
With the Longshoremen deadline still weeks out, any contingency moves taken by retailers at this point are precautionary. However, planning for it ahead of the busiest shopping season of the year might help save costs and sales if things turn awry.
“No one can plan for labor strikes so companies begin to scramble,” Johnsen said. “Last minute surprises are expensive … operational costs can go up, customer service and revenue can suffer ... if [retailers] don’t get products to shelves, they’re hurting their top line.”