Manufacturing’s future is where the jobs are: Johnson Controls CEO
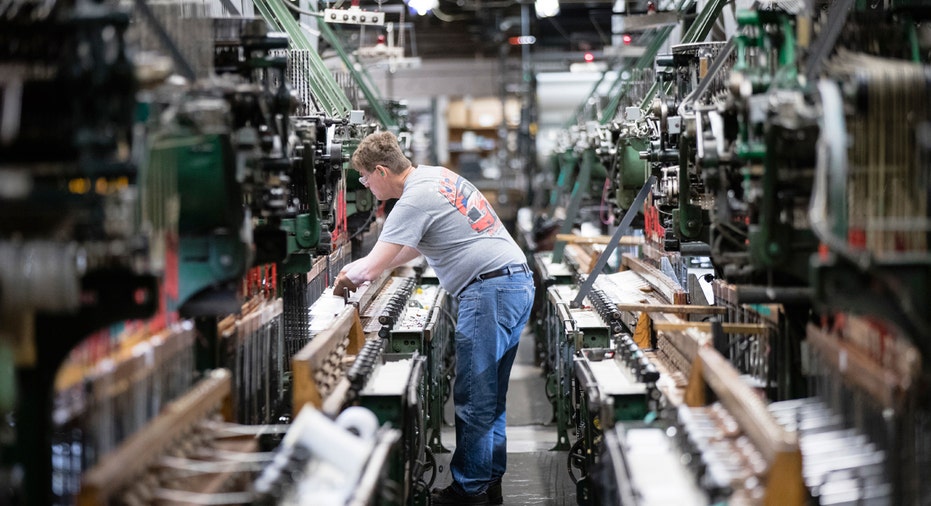
The U.S. job market is one of the many sweet spots of the economic recovery now underway. On Thursday, President Trump is expected to sign an executive order to create a group focused on improving workforce training.
American workers are witnessing a record streak of job growth, historically low unemployment and high optimism. Still, to some, all this good news is tempered by what they perceive as high-tech threats on the horizon: radical technological advancements in areas such as artificial intelligence (AI), machine-to-machine communication and the Internet of Things (IoT), which are changing the way we do just about everything in powerful ways. This has had a particularly strong impact on manufacturing.
The industry is ushering in a new era of smart manufacturing, where machines, processes and people are connected to maximize value. In addition to the benefits, these changes have created uncertainty about jobs and what intelligent factories and the rise of machines means for the workforce. This uncertainty is warranted: rapid technological advancement will cause disruption and will likely necessitate workflow changes across all organizational levels, from senior leaders to manufacturing shop-floor employees.
Still, it is a mistake to focus too much on what may be lost and miss what is being gained. Unemployment rates in the United States are at lows rarely seen in the last half a century and research from Gartner suggests that by 2020, artificial intelligence will create more jobs than it eliminates, leading to approximately two million net-new jobs by 2025. Today there are already more high-paying jobs in emerging technical fields than there are qualified applicants to fill them and that gap will continue to grow as new technologies are adopted more broadly.
The current administration has been a vocal proponent of job training and workforce development to create jobs and help fill the growing tech-skills gap, explicitly calling for the expansion of vocational education. President Trump has also signed a Presidential Memorandum directing the Department of Education to increase access to high-quality science, technology, engineering, and mathematics (STEM) education and his administration’s most recent budget request for 2019 makes a strong push for further investment in high school-based apprenticeships and career and technical education.
These are important steps in the right direction. As it currently stands, neither our educational system nor workforce are prepared to meet the demands and capitalize on the opportunities ahead of us, but they can be if we act now to prioritize STEM education, vocational training and workforce development.
Johnson Controls has deep roots in manufacturing starting in 1885 when Warren S. Johnson founded the company after inventing the first electric room thermostat, for which he was recently inducted into the National Inventors Hall of Fame. Following his legacy, we create energy efficient products and solutions that help buildings, vehicles and energy systems deliver on the promise of smart cities and communities. Certain elements of our manufacturing system and business model, like putting the customer at the center of everything, ensuring a stable production environment, organizing around customer pull and exercising zero tolerance for waste, are always constant. Yet over the last hundred-plus years, the breadth of our product and technology portfolio have changed dramatically, and so have our factories and workforce. Our new Johnson Controls Advanced Development and Engineering Center in York County, Pennsylvania, is the newest and most advanced engineering and testing facility for chillers in the world. But we believe you can’t just invest in technology.
Ticker | Security | Last | Change | Change % |
---|---|---|---|---|
JCI | JOHNSON CONTROLS INTERNATIONAL PLC | 68.78 | +2.07 | +3.10% |
We rely on a highly technical workforce to create the intelligent buildings, efficient energy solutions and integrated infrastructure systems that power smart cities and communities around the world. As major employers and the organizations implementing automation, AI, IoT and machine-to-machine communication systems at scale, large corporations have a responsibility to help build and support the technical workforce of the future.
The Education Gap
At a time when the United States has over half-a-million open technology jobs, our schools and universities are producing hardly one-tenth that number of computer science graduates. The result is a growing high-tech skills gap that hurts job seekers and employers. In this environment, students and workers of all abilities and from all backgrounds can benefit from high-quality career and technical education, both thorough formal vocational training and a variety of free, self-educational resources. However, to get there the private sector needs to step up to the plate. At Johnson Controls, we’ve partnered with Lincoln Tech, a leading provider of specialized technical training, to provide expanded career opportunities for graduates and help lay the foundation for the workforce of the future by providing the essential training needed to be successful in a technical career.
Of course, technology revolutions are not painless. Many industries will face tough transition periods as workflows and the labor force adapt. But they also represent a tremendous opportunity for U.S. manufacturing and the broader economy. Rapid technological advancement is already creating new opportunities in growing sectors like the HVACR market. The Bureau of Labor Statistics has projected employment of HVACR workers to grow 15 percent from 2016 to 2026, much faster than the average for all occupations, and that 11,500 new workers will need to be trained by 2022 to meet anticipated demand. These are good-paying jobs that in most cases don’t require a bachelor’s degree.
Technological advancements are creating more career opportunities for workers with skills in areas like solar thermal heating, green HVAC mechanics, digital controllers and building automation. It has also opened up new career paths in manufacturing and created a growing need for data scientists and specialized workers with the analytical and business skills needed to translate data-driven insights into actionable strategies.
For employers and employees in a wide range of fields, the opportunities associated with technological transformation are greater than the costs associated with workforce realignment. The reality is that cost of retraining and “upskilling” existing employees is often lower than hiring new ones, and for many, it will provide a welcome opportunity to learn new, career redefining skills that will continue to open new doors.
Now is the time for more investment in workforce development, job training and a system of vocational education in the STEM fields that will define and empower the economy of our future. Investments in our workforce are investments in our economy, security and prosperity that will serve us well now and in the future.
George R. Oliver is chairman and CEO of Johnson Controls. Prior to becoming CEO on Sept. 1, 2017, he served as president and chief operating officer with responsibility for the company’s operating businesses and leading the integration of Johnson Controls and Tyco following their September 2016 merger.
*This article was originally published on 7/5/18.