Why Your Business Needs an Injury and Illness Prevention Program
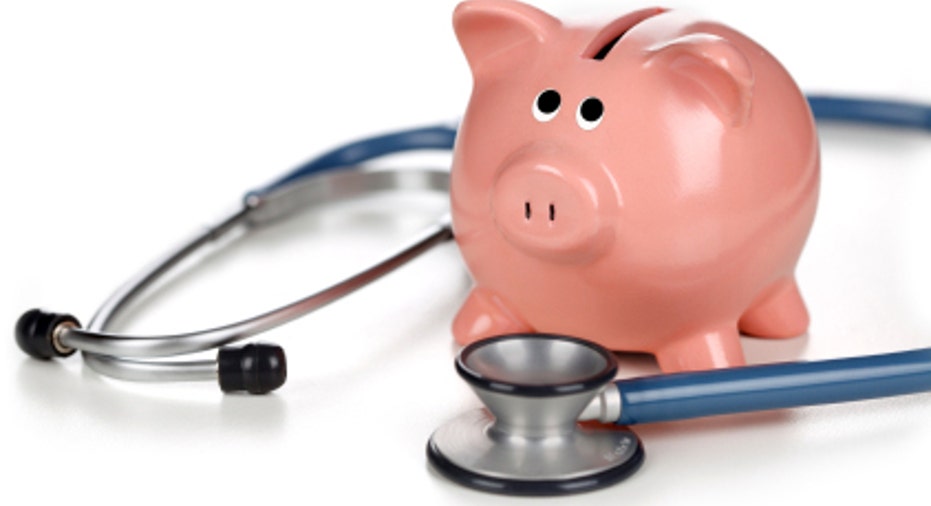
Worker safety should be a priority for businesses large and small, but ensuring the safety of employees doesn't have to cost small business owners a ton of money. In fact, according to one expert, it doesn't have to cost a dime.
Implementing injury and illness prevention programs in the workplace can protect small business owners from losing money through worker's compensation payments and lawsuits. They can also help keep productivity in the workplace, according to Woody Hill, vice president, Loss Control for EMPLOYERS.
"Small businesses are not as likely to be able to replace that body or individual because of the economy," Hill said, emphasizing the importance of having such prevention programs in place. "We also have an aging workforce, with people working later into life than ever."
Hill recently conducted a webinar for the National Federation of Independent Business called "Controlling Workers' Compensation Costs Through Injury and Illness Prevention Programs" that detailed how employers can create and implement programs.
The impact of injury and illness occurrences can take their toll on a business. According to the Bureau of Labor Statistics, approximately 3.3 million serious work-related injuries and 4,300 fatalities occurred in 2009. The direct cost of the most disabling workplace injuries and illnesses in 2008 cost $53.42 billion in workers' compensation costs, totaling more than $1 billion a week, according to Liberty Mutual's 2010 Workplace Safety Index.
Today there are 15 states across the country that require written injury and illness prevention programs for businesses, Hill said. Small employers need to read their Occupational Safety and Health Administration (OSHA) handbook documents to make sure they are compliant with requirements. Implementing such a program should be of little or no expense, according to Hill, and shows the employer values his or her workers.
"Partner with your insurance carrier, get your program templates from them," he said. "OSHA has a plan builder which is confidential and helps build a compliant program."
Having such programs in place are also of great importance for workers themselves. According to a recent survey, "Financial Security for Working Americans: An Economic Analysis of Insurance Products in Workplace Benefits Programs," 1 in 3 individuals will be disabled for at least six months during their earning years. What’s more, the survey also found 7 in 10 American households could not pay their normal living expenses if a wage earner were disabled for that amount of time.
The survey, commissioned by disability insurance provider Unum and conducted by Charles River Associates, found that only 32% of workers are covered by long-term disability insurances, which costs about $25 a month in group disability premiums.
Here are the four key elements of an injury and illness prevention program for small business owners.
No. 1: Management leadership and employee participation: Hold managers accountable for carrying out safety and health responsibilities in the workplace, and provide them with the authority to do so. Also, provide employees with the opportunity to participate in establishing, implementing and evaluating the program.
"Without the worker buy in, it won't be an affective program," Hill said. "Management needs to be supported and maintain their drive."
No. 2: Hazard identification and assessment: Before any new equipment, materials or procedures are put in place, owners should asses their potential hazards.
This also applies to conducting worksite inspections and reviewing safety and health information. Also assess the severity of these hazards.
"It's not just a matter of identifying the hazard, but also document what you have to do to prevent it," he said.
No.3: Education and training: Provide your employees with information and training as part of your injury and illness prevention program including identifying hazards and how they are controlled.
"[Employees] have to be trained in language that they understand, especially in a bilingual workplace," Hill said. "Most employers just assume [workers] understand what is being communicated."
No. 4: Evaluate program effectiveness: At least annually or whenever new substances, processes, procedures or equipment are introduced into the workplace, owners need to evaluate their worker safety program. A review should also be done whenever the employer is made aware of a new or previously-unknown hazard.
Most importantly, Hill said businesses need to hire smartly and train their new workers from day one in such programs.
"Train them out of the gate so you don't have a mishap."
To learn more about OSHA's Safety Pays Program, please click here and to view the NFIB Webinar click here.